Global Network of Specialists
Longer, More Flexible Life for Operating Assets
Enerflex understands the complexities of natural gas processing, cryo, refrigeration, compression, and electric power equipment in every possible configuration. So we’re the natural choice for retrofit, rebuild, and reconfiguration in our shops or in the field — anywhere around the world, in any application, even when timelines are short.
Enerflex’s designers, project managers, and engineers are innovative and flexible in their approach to cost-efficiency and optimization, because every retrofit project requires an innovative solution. Extending the productive life of assets as conditions change, maximizing horsepower utilization, meeting new emissions targets, debottlenecking, or even decommissioning — we do it all.
World-Class Field Teams
When the project hits the hands of our field teams, we are in a league of our own. Our extremely talented and professional teams ensure a safe, reliable outcome of any project.
If it’s not possible to retrofit in the field, the unit can be dismantled and serviced at one of our local branches. Enerflex will also provide a short-term rental from our fleet as a stop-gap to minimize downtime. If you have any questions about the performance of your equipment, reach out to our technical sales and applications team.
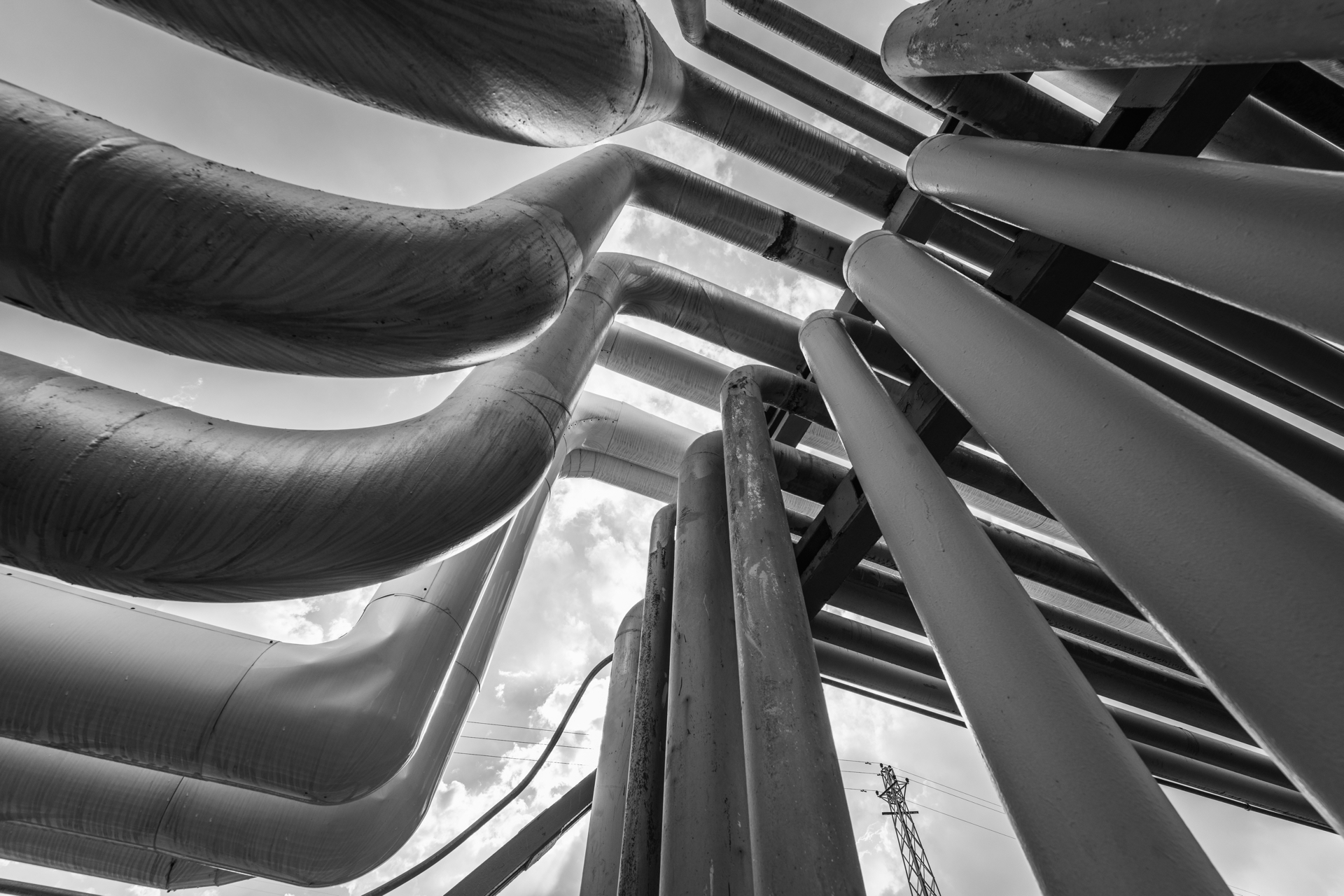
The Enerflex Advantage
- Retrofitting your existing equipment is often considerably less expensive than buying a new package, plus it will be delivered in a fraction of the time.
- We aim to achieve 100% compression horsepower use. By balancing costs against benefits on every job, we strive to minimize your operating overhead and maximize capital efficiency.
- A fully integrated and dedicated group of retrofit experts with unmatched industry depth in engineering, design, overhaul, and service — and thousands of successful retrofits completed.
- Our engineers are renowned for their ability to innovate and find the most cost-effective way to modify or upgrade your equipment to optimize the efficiency and increase uptime / productivity of your existing installation.
Enerflex in Action
- Carrot Creek, Edson, Alberta
1,478 HP / 1,200 RPM Sweet Gas, High Pressure Injection
Enerflex was commissioned to retrofit a 2004 fleet Waukesha 7042GSI – Ariel JGK 4/3 into a high-pressure injection unit (4,000 psig discharge). This was a multi-stage retrofit that required overhead cranes because the cooler and interconnecting pipe modules were too heavy to lift by hand.
The rebuild was complex and needed to be staged. The engine, compressor, and all rotating equipment was overhauled, with upgrades to every peripheral part of the unit. Enerflex teams fabricated new process spooling across all three stages of compression, four new pulsation bottles, new two- and three-stage suction scrubbers, and three new IC1, IC2, and AC cooler sections. In addition, three cylinders were replaced, a B149.1 fuel train upgrade was completed, and new process pressure transmitters were installed, alongside a new control panel.
All pressure vessels, spooling, and cooler sections were updated to ABSA, and acoustic and torsional studies were completed with QC documentation.
Outcome
The project was completed in under four months. It has a P.Eng-stamped PID, complete with a line list. The project wrapped-up with a test run, full third-party inspection, and unit dismantling and loading onto three trailers — all with zero incidents.
- Tucker Thermal Plant, Cold Lake, Alberta
Field Retrofit to Meet New Field Conditions
Enerflex re-cylinder retrofitted an unusual single-stage, two-throw Dresser Rand compressor unit. The existing cylinders were replaced onsite with new customer-supplied cylinders, requiring new pulsation bottles and piping to accommodate the new cylinder connections, all tied seamlessly into an existing first stage scrubber. The new unit produces 450 HP at 1,800 RPM.
Outcome
The local Enerflex service team faced challenges of complex geometry and high manufacturing tolerances on an unusual piece of equipment. To mitigate risk, the Enerflex solution has separate suction pulsation bottles on each cylinder, connected with the single line coming out of the scrubber. The design was 100% pre-fabricated in the shop with smaller spool pieces, enabling fit-up in the field without rework.
Enerflex conducted a safety inspection of the existing unit before bringing it back into service. The team also installed two code-compliant discharge PSV’s to avoid the expense of upsizing an existing vent header and off-skid piping. This led to cost-savings for the client.