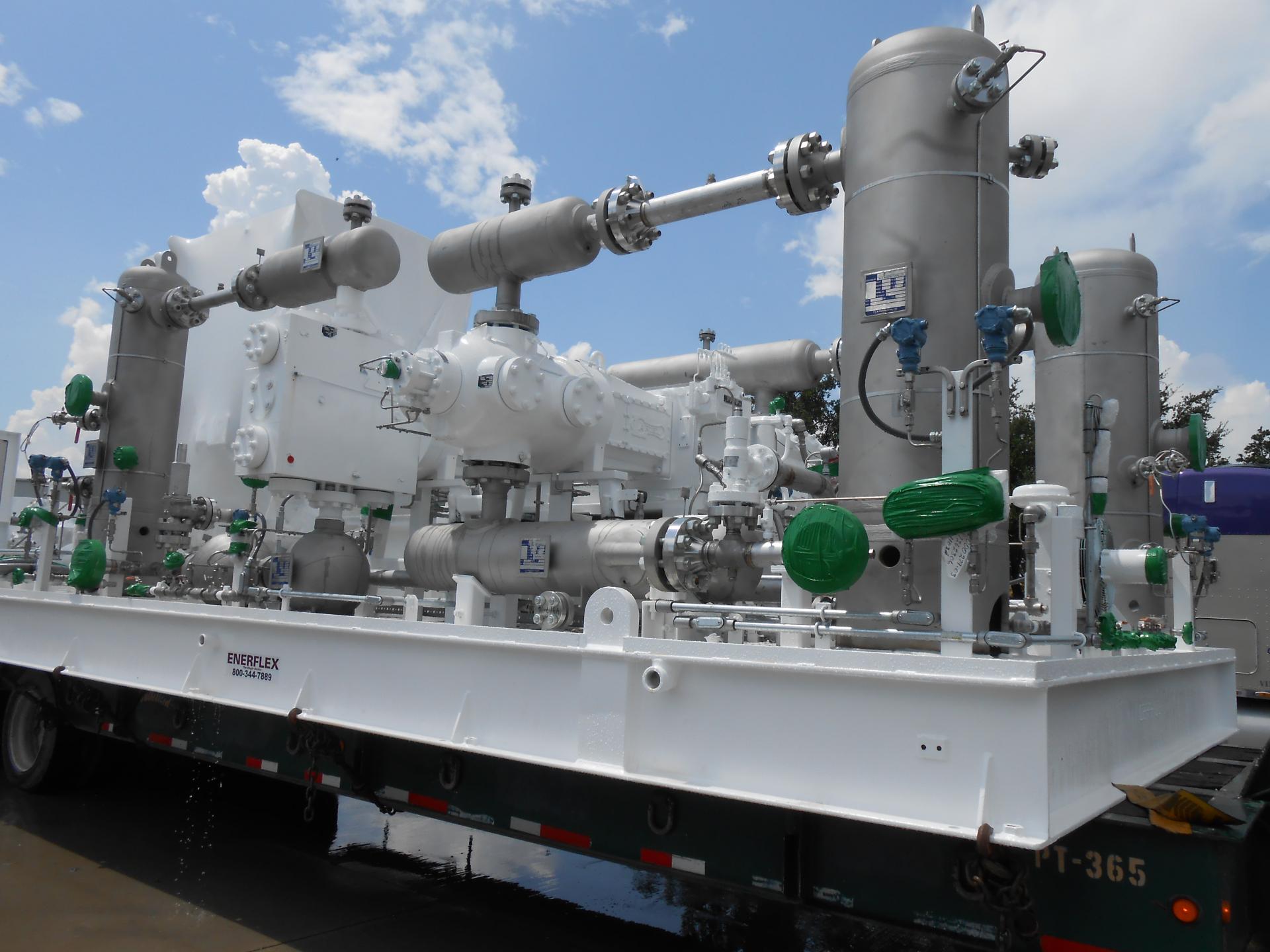
Equipment / Compression
Process Compression
Optimized Gas Conditioning for Onshore and Offshore Operations
Our process compression solutions integrate seamlessly into your operations and are fully supported by end-to-end service capabilities.
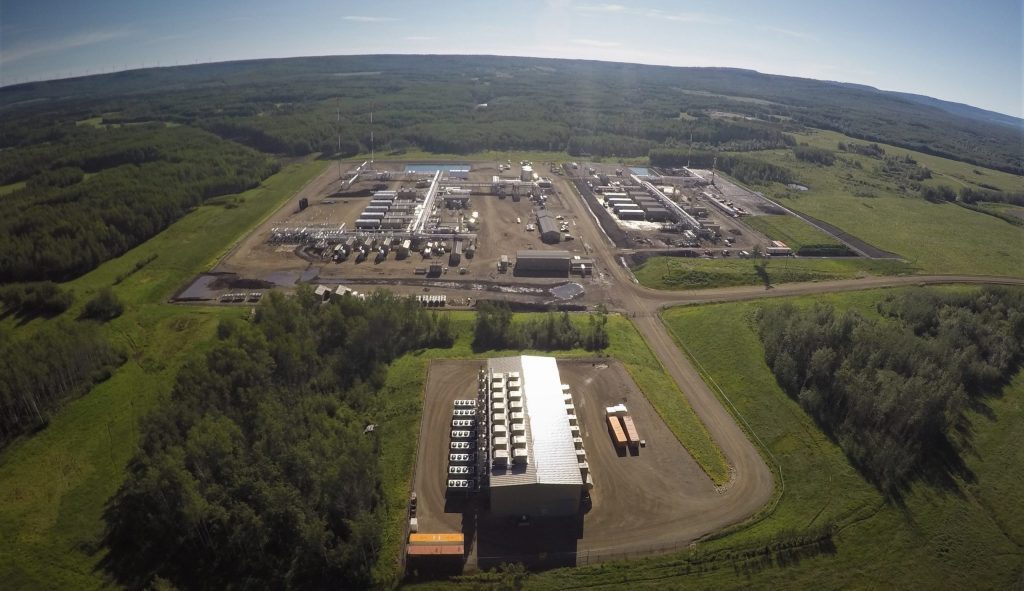
Process Compression Benefits
We ensure precise control of gas pressure for natural gas processing plants, optimizing both intake and output to meet exacting specifications and deliver reliable results using reciprocating, rotary screw, centrifugal, blower or sliding vane technologies.
Solutions
We develop all major forms of process compression, including:
- Hydrogen
- Helium
- Methane
- Nitrogen
- CO2
- Chlorine
- Sour Gas
- Acid Gas Reinjection
- Digestor and Landfill Gas
- Boil-Off Gas
- Fuel Gas Boosters
- Process Air
- Instrument Air
- Syngas
- PSA Feed and Tail Gas Compressors
The Enerflex Edge
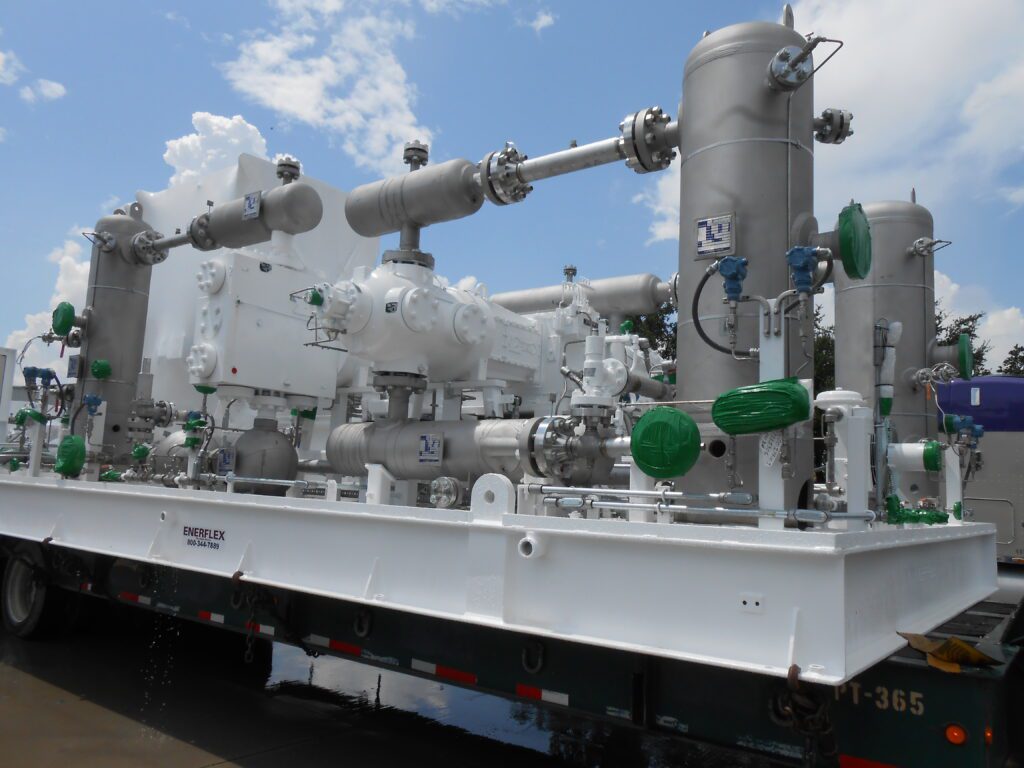
Offshore and Onshore Compression Expertise
We provide fully integrated compression systems for offshore and onshore applications, designed to recover or re-inject associated natural gas efficiently. Our process solutions meet regulatory requirements where flaring is restricted or pipeline access is unavailable.
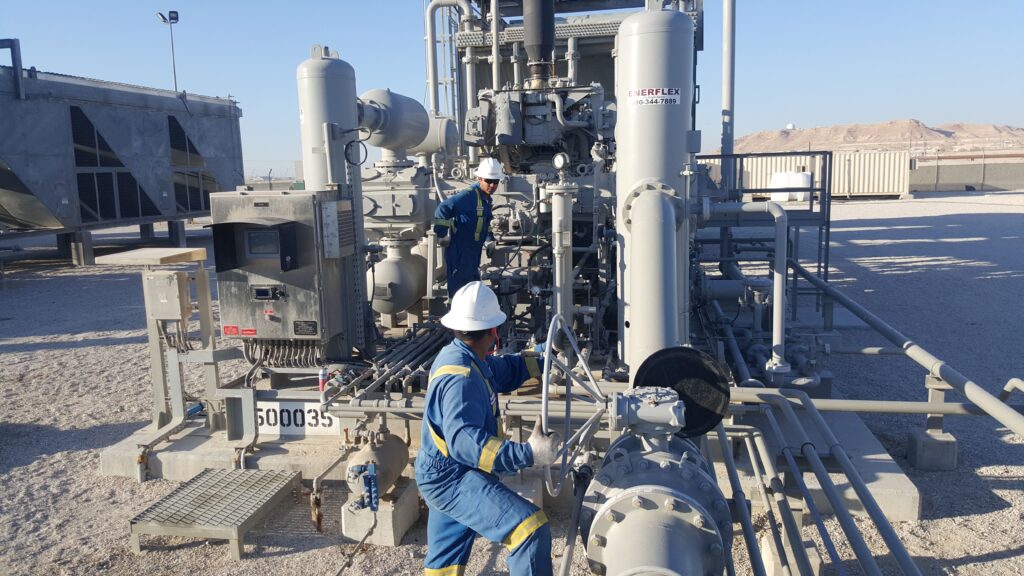
A Full-Service Partner with a Complete Portfolio
Our end-to-end solutions cover the entire lifecycle of your project. We offer a complete suite of services—from engineering and design to installation and commissioning—ensuring your operations run seamlessly and provide optimal performance.
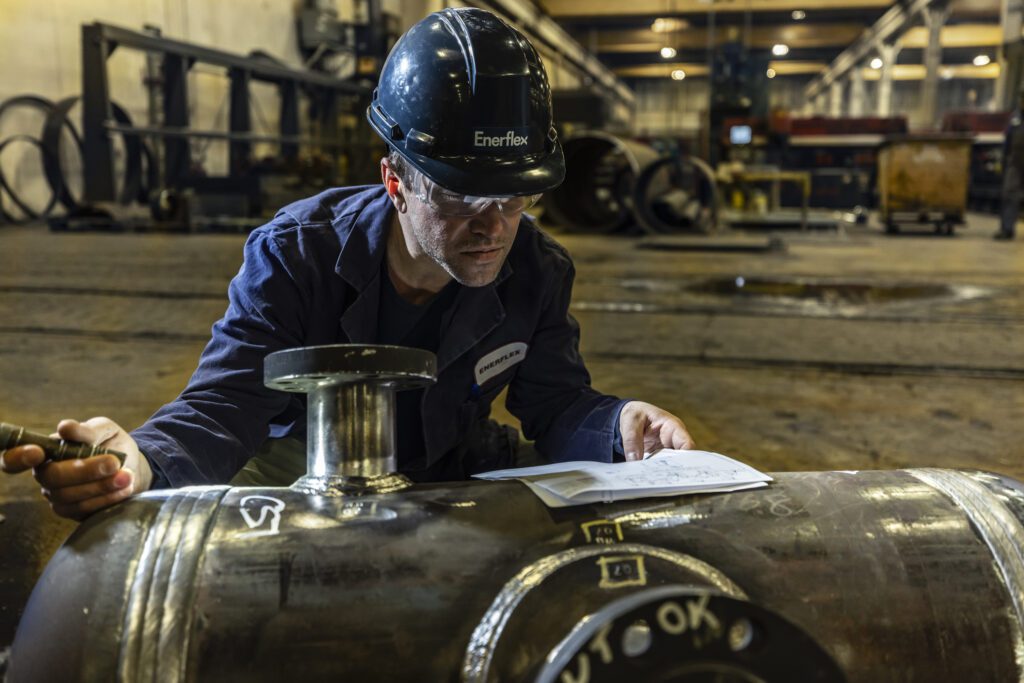
Unmatched Safety Standard
We pride ourselves on industry-leading safety records, ingrained in our culture and embedded in every project we deliver. With stringent manufacturing standards at the core of our process, we ensure top-tier equipment quality and operational safety.
Case Study
Boil-Off Gas Compressor and Ethylene Terminal
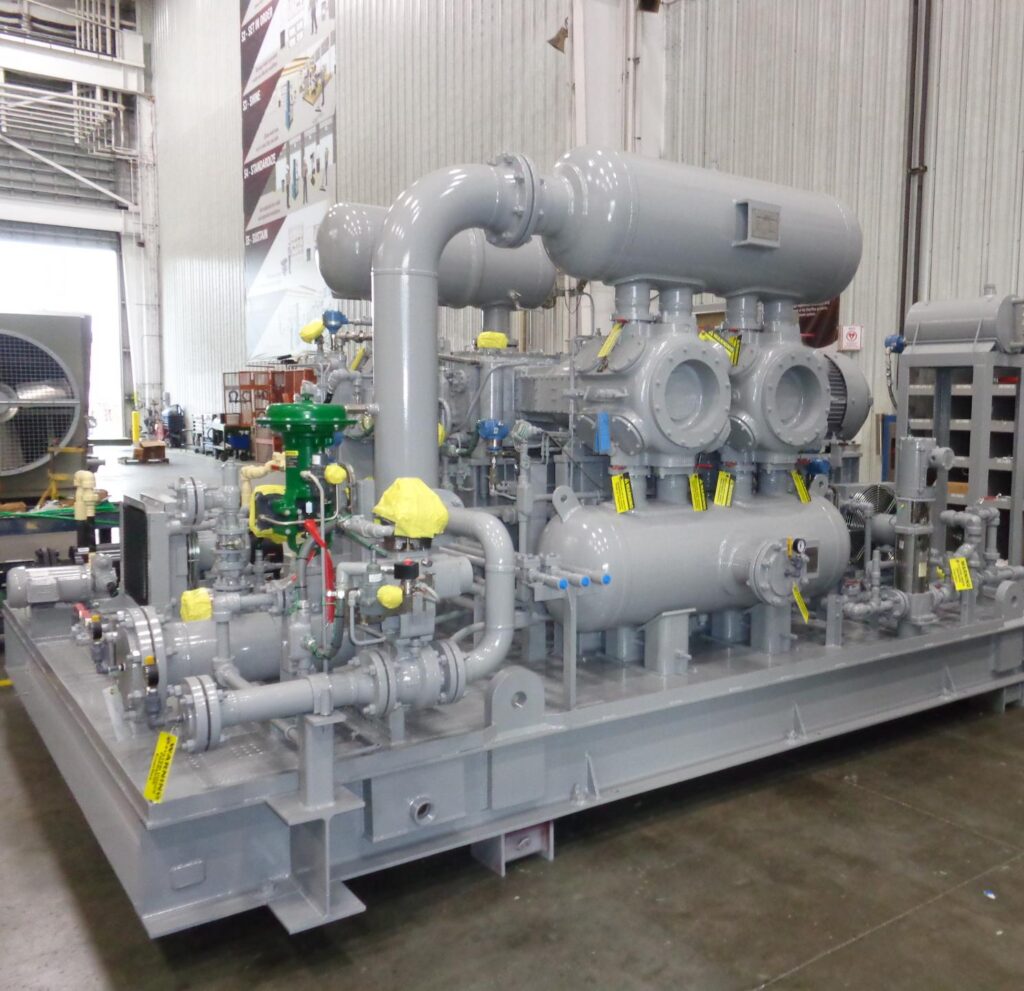
Challenge:
Enerflex partnered with a key customer in Morgan’s Point, Houston Ship Channel, Texas, to install two Ariel KBK/6 three-stage reciprocating compressors, customized to fit a small site footprint. The project required precise modifications to reduce vibration and optimize performance.
Solution:
We customized the compressors, performing torsional and acoustical DA3 analysis, and provided 24-hour commissioning services. The package included pneumatic cylinder and valve unloaders, packing water cooling, non-lube cylinders, and a full range of on-skid components.
Outcome:
The project was completed on-time, under budget, with all contractual requirements met within an eight-month timeline.
Case Study
Sour Service Injection Compressor for Oil Well Reclamation
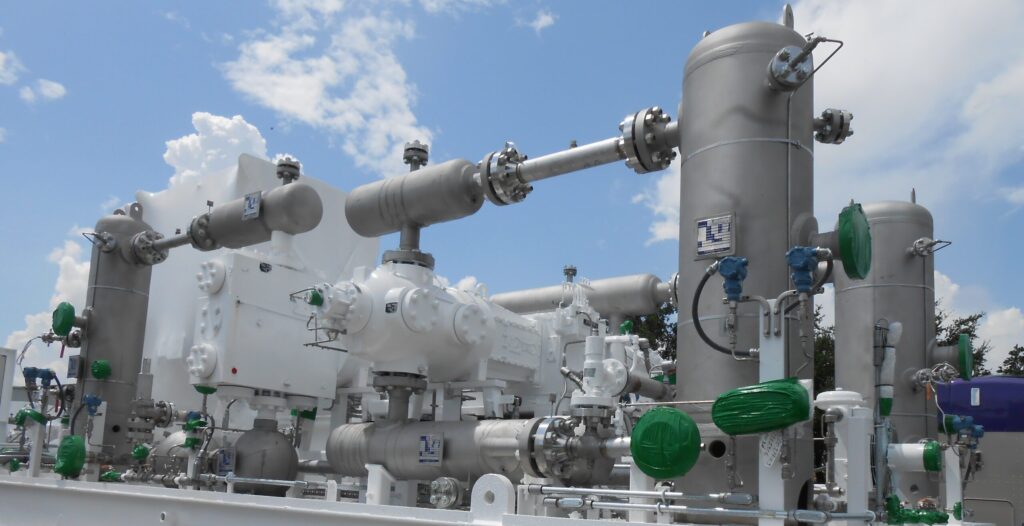
Challenge:
In Charlotte, Texas, Enerflex supplied two JGA/2 compressors with tandem cylinders, designed for sour service, as part of an oil well production upgrade. These compressors reinjected sour gas back into oil wells to enhance recovery.
Solution:
The compressors, driven by 350 HP Toshiba electric motors, utilized a variable frequency drive to handle a speed range of 900 to 1,800 RPM. The units were equipped with remote monitoring for operator safety and designed for a maximum discharge pressure of 9,000 psig.
Outcome:
We successfully addressed installation challenges, including managing higher-than-expected H₂S content and debris in the gas stream. With safety protocols in place, the project was completed efficiently, ensuring enhanced oil production.
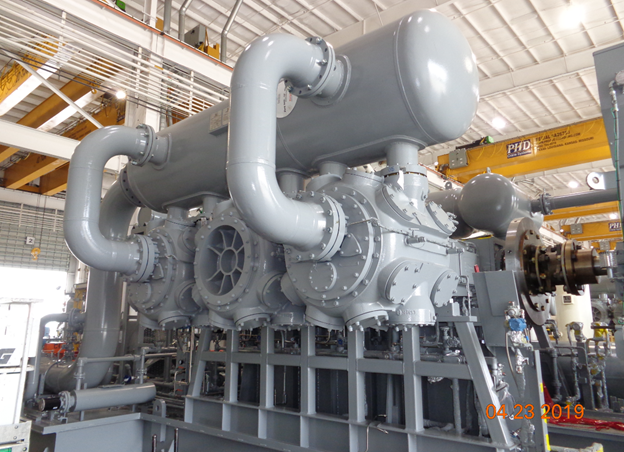
Custom Process Compression Systems
We develop custom process compression systems for offshore compression on floating production, storage, and offloading vessels (FPSOs), or other onshore/offshore units used to recover or re-inject associated natural gas.
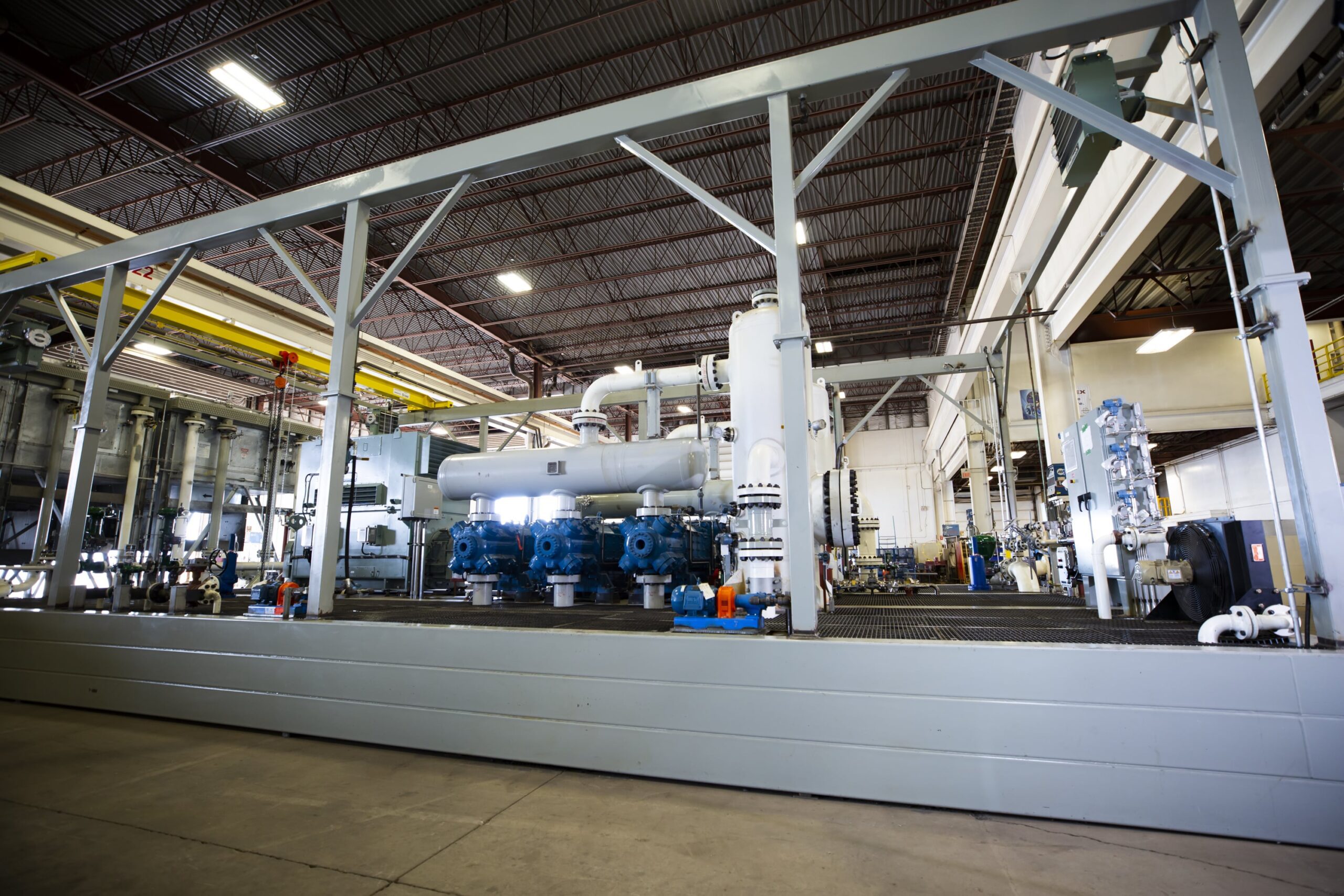
Pre-Engineered Process Compression Systems
We offer pre-engineered process compression systems for rapid deployment, with flexible options tailored to your needs.